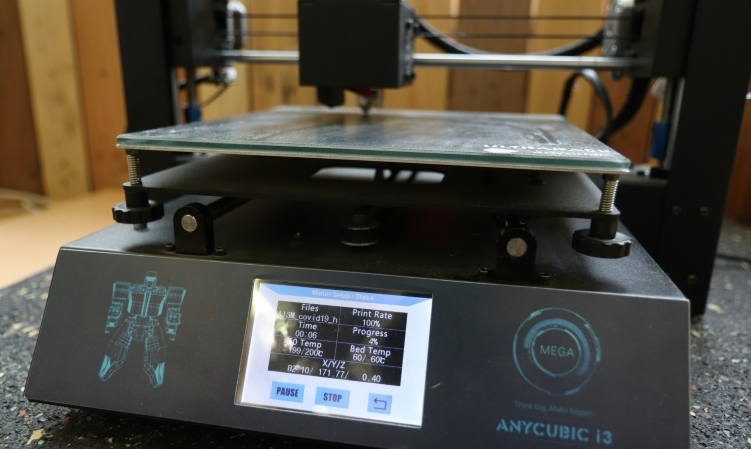
By Tom BARFIELD
DARMSTADT, Germany (AFP) — The high-ceilinged workshop in Darmstadt is usually open to anyone — from hobbyists trying new machinery or techniques to high-tech startup workers tinkering with prototypes.
During the coronavirus pandemic, it has been turned into a hub for dropping off plastic parts made at home by volunteers and used to assemble face shields they are sending to health workers across Germany and even as far off as a refugee camp in Greece.
The so-called German MakerVsVirus network — extending into Austria and Switzerland thanks to the shared language — gathers about 7,000 enthusiasts who are using their own 3D printers or other gadgets to produce much-coveted medical gear.
With medical workers worldwide scrambling for protective shields, masks or gowns amid a huge shortage because of the coronavirus, the tech geeks have stepped in to help fill the gap.
Physicist Nico Neumann, who has converted the drop-in workshop into the MakerVsVirus hub, said: "For me, it started with five face shields for my uncle's medical practice.
"Then my grandfather's care service wanted some, and then we noticed that there was this network in Germany" which was ready to be mobilised."
"We started out as a lot of private individuals and lone wolves who wanted to help," he added.
By late April, Neumann and his team had delivered around 1,600 shields to users in the region.
The figure is even more staggering if the contributions from all 180 MakerVsVirus hubs across Germany are taken into account — some 100,000 face shields have been sent out in the last weeks.
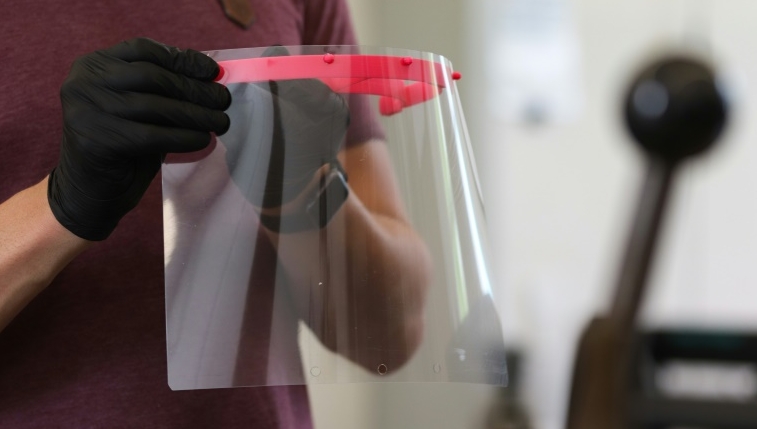
'Overwhelming'
Offloading dozens of plastic parts fresh from the 3D printers at his firm outside the city, Stefan Herzig said: "This situation is really overwhelming for everyone.
"It's a nice feeling being able to help, even if my contribution is relatively small."
The parts were laid on tables at the entrance of the workshop bearing neatly printed labels for new and fulfilled order documents, freshly delivered plastic parts and assembled face shields ready for delivery.
Each face shield comprises a flexible transparent sheet, anchored at top with a 3D-printed plastic part and secured around the head with an elasticated band. Another 3D-printed plastic part at the bottom helps the mask keep its shape.
Although some homemade components turn out fragile or misshapen, those up to standard are sturdy enough to withstand disinfection and repeated use.
Beyond helping medical and other institutions, a shipment of face shields has even reached the notoriously overcrowded and vulnerable refugee camp on the Greek island of Lesbos.
The online organisation brought together "all these different characters" who are adept at finding technical solutions to create much-needed equipment, said Neumann.
He himself has to organise his voluntary work around a full-time job developing optics.
"I'm not getting much sleep or having much of a weekend," Neumann said.
Flexible
With more professional firms increasingly stepping in to fill large orders for face shields, the former hobbyists are now tackling small batches and more specialist items.
New offerings include an adaptor to fit dispensers from one disinfectant brand onto containers from another as hospitals use whatever supplies they can find.
Another is a plastic hook to relieve the strain on sore ears from wearing facemasks all day.
"In this environment where it's almost in our spare time, we can respond more flexibly than if you had to convert a whole company's production," Neumann said.
"These are things where we can help quickly with our 3D printers."
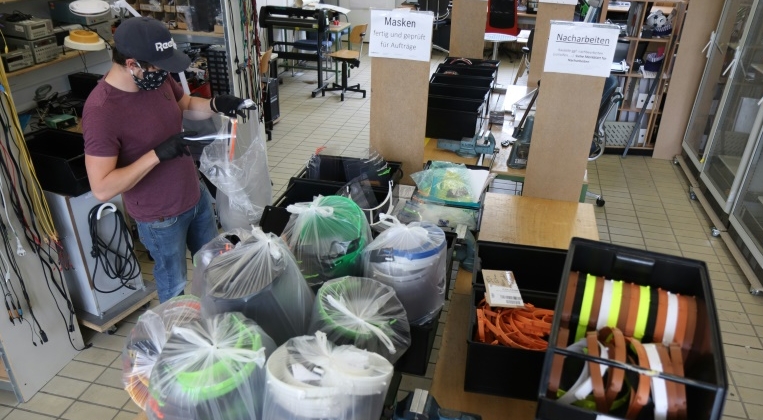
ADVERTISEMENT
ADVERTISEMENT




