DENVER: As Americans struggle under backbreaking rental prices, builders are turning to innovative ways to churn out more housing, from 3D printing to assembling homes in an indoor factory to using hemp – yes, the marijuana cousin – to make building blocks for walls.
It’s a response to the country’s shortfall of millions of homes that has led to skyrocketing prices, plunging millions into poverty.
“There’s not enough homes to purchase and there’s not enough places to rent. Period,” said Adrianne Todman, the acting secretary of the U.S. Department of Housing and Urban Development under former President Joe Biden.
One way to quickly build more is embrace these types of innovations, Todman said.
“I can only imagine what our housing situation would be like now if we could have made a decision to be more aggressive in adopting this type of housing” decades ago.
So what are these new ways of building homes? And can they help reduce the cost of new housing, leading to lower rents?
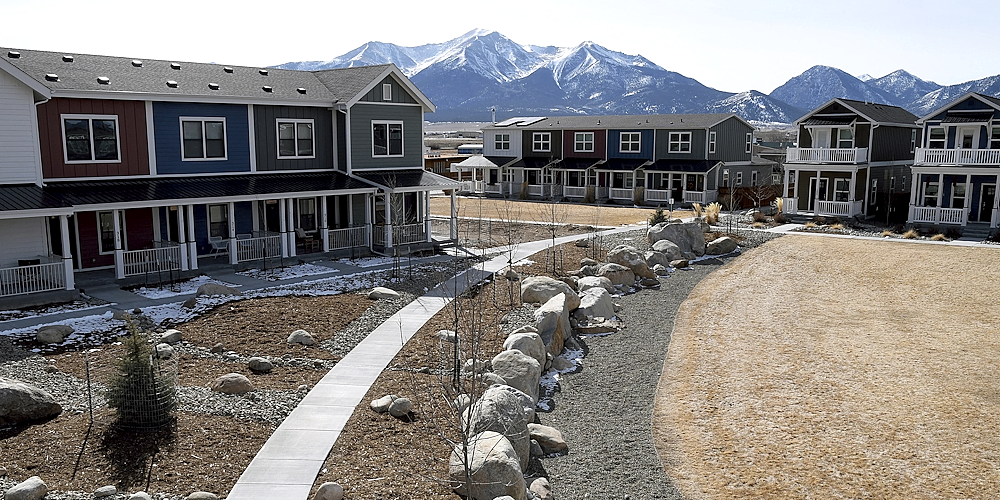
Factory-built housing put together in a week
In a cavernous, metal hall, Eric Schaefer stood in front of a long row of modular homes that moved through the plant, similar to a car on an assembly line.
At a series of stations, workers lay flooring, erected framing, added roofs and screwed on drywall.
Everything from electrical wiring to plumbing to kitchen countertops were in place before the homes were shrink-wrapped and ready to be shipped.
The business in the Colorado Rocky Mountains, Fading West, has pumped out more than 500 homes in its just over three years of operation, each taking just five to seven days to build, even in the coldest winter months, Schaefer said.
Once assembled in the plant, the narrow townhouse-style homes with white trim, balconies and front porches, are about 90 per cent done.
At their final destination they are move-in ready within six weeks, Schaefer said.
The company works with towns, counties and housing non-profits to help address the shortage of affordable homes, mostly for workers who’ve been squeezed out by sky-high prices in ritzy mountain towns.
That includes Eagle, Colorado, not far from the Vail ski resort, where Fading West worked with Habitat for Humanity to install modular homes at affordable rents for teachers and other school district employees.
The homes tend to be on the smaller side, but can be multifamily or single family.
“You can build faster. The faster you build – even at a high quality – means the lower the price,” Schaefer said.
“We see this as one of the pieces to the puzzle in helping solve the affordable housing crisis.”
There’s a hefty upfront cost to build the factory, and part of the challenge is a lack of state and federal investment, he said.
A patchwork of building codes governing how a structure can be built also makes it difficult, requiring changes to the construction depending on the town or county it is being sent to.
Manufactured housing is similar to modular housing, but the units are constructed on a chassis – like a trailer – and they aren’t subject to the same local building codes. That’s part of the reason they are used more broadly across the U.S.
Roughly 100,000 manufactured homes were shipped to states in 2024, up from some 60,000 a decade earlier, according to Census Bureau data. Estimates of modular homes built annually often put them below 20,000.
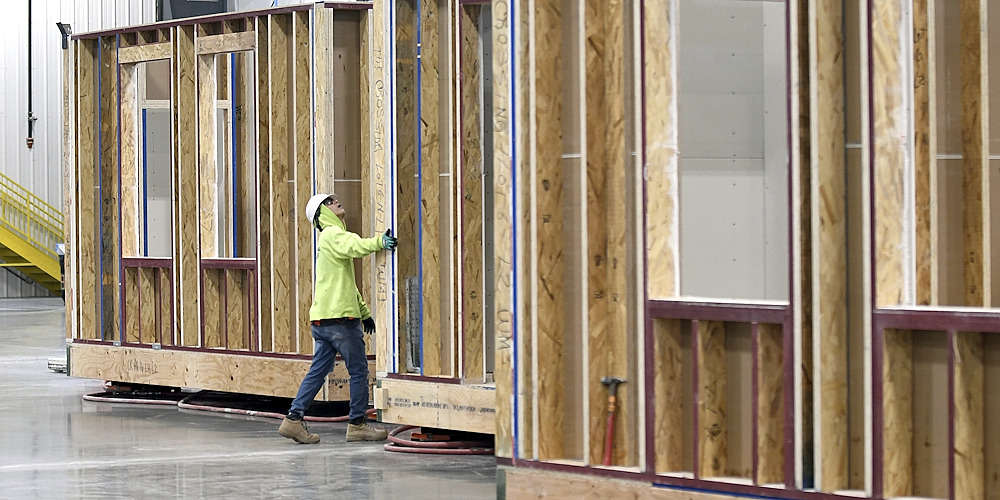
3D printing is innovative but still ‘a long game’
Yes, there’s technology to 3D print homes.
ADVERTISEMENT
ADVERTISEMENT




